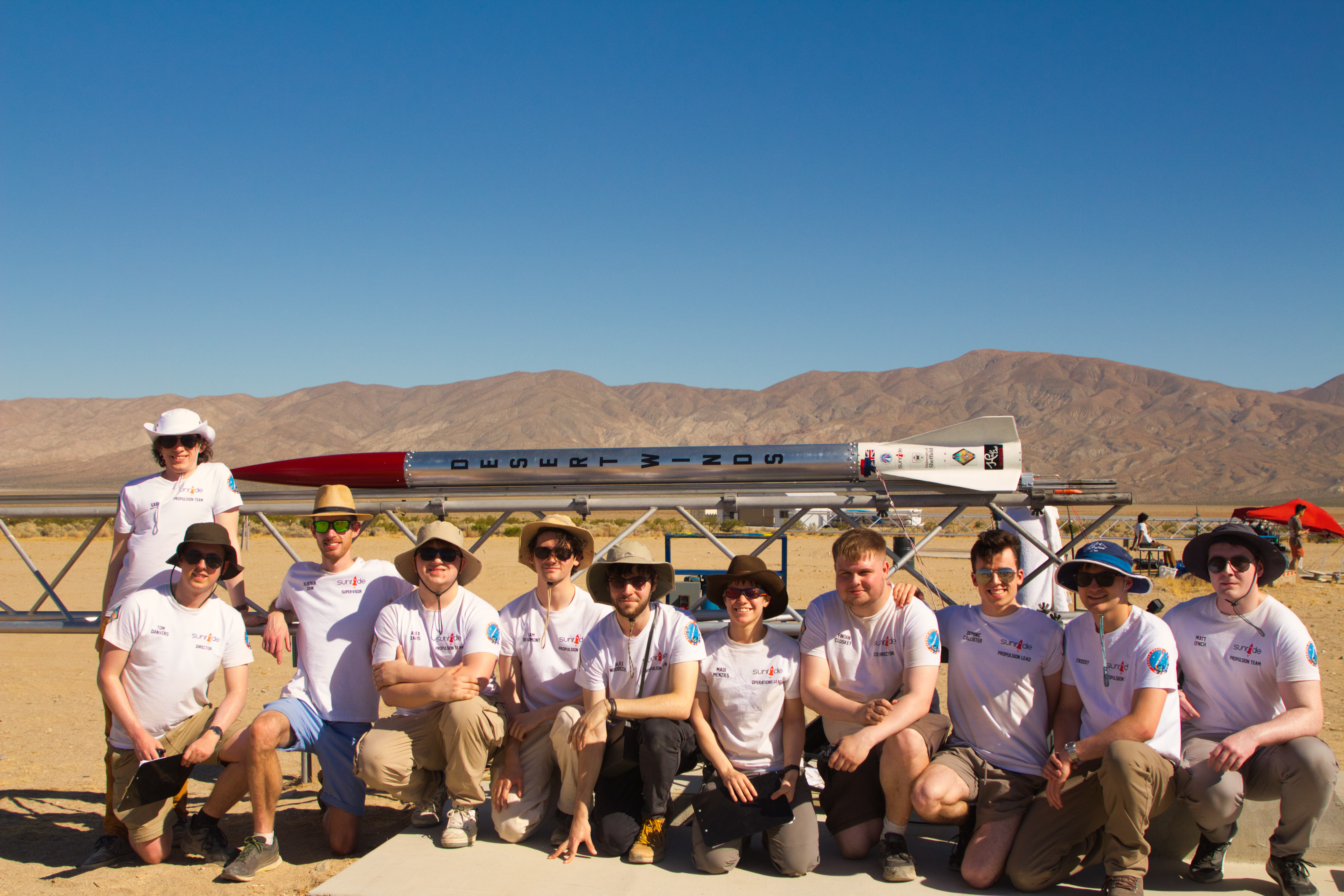
DESERT WINDS
The UK’s first amateur liquid rocket – launched June 2024
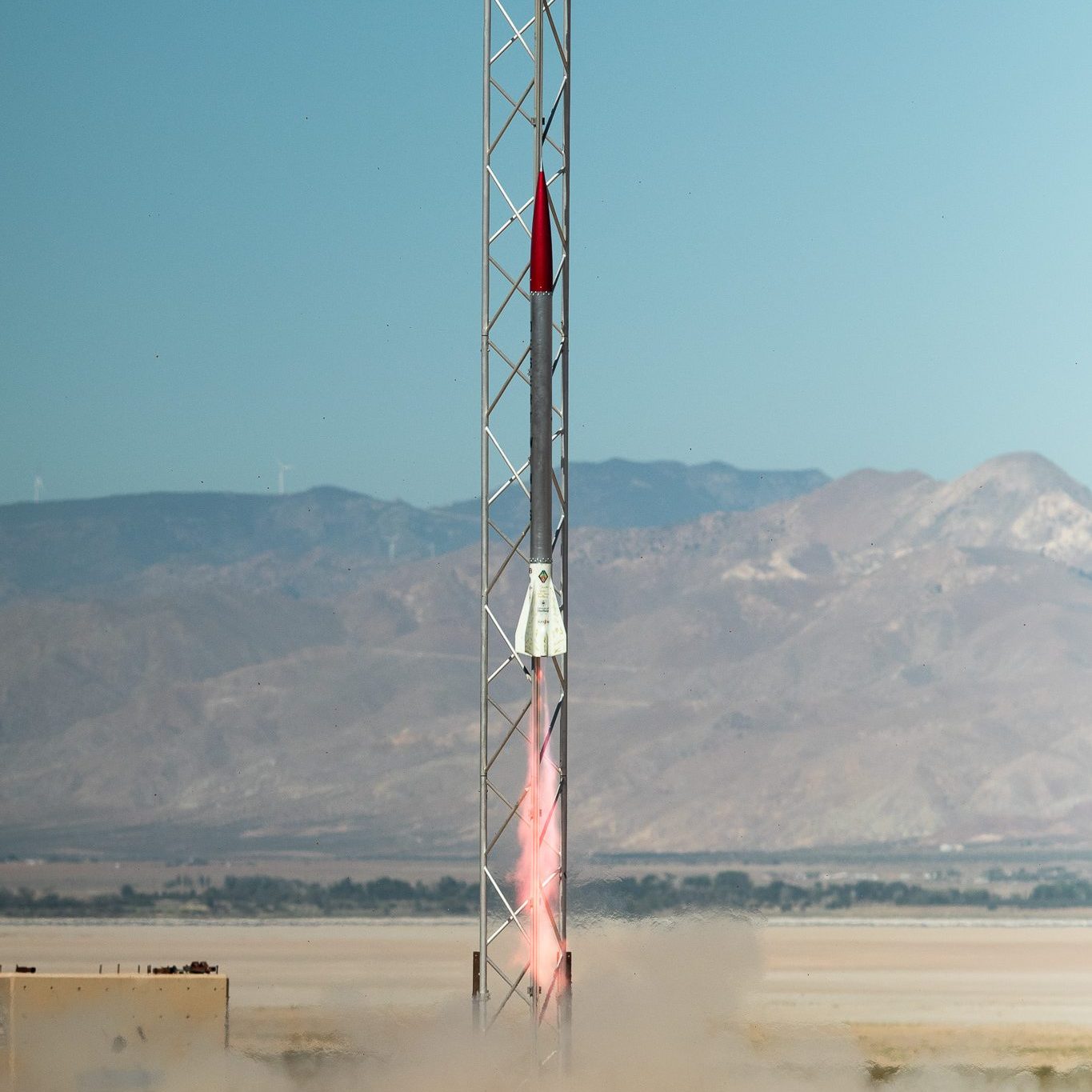
“Desert Winds” was Sunride’s first liquid fuelled rocket and has become the first liquid fuelled rocket to be launched by a UK student team.
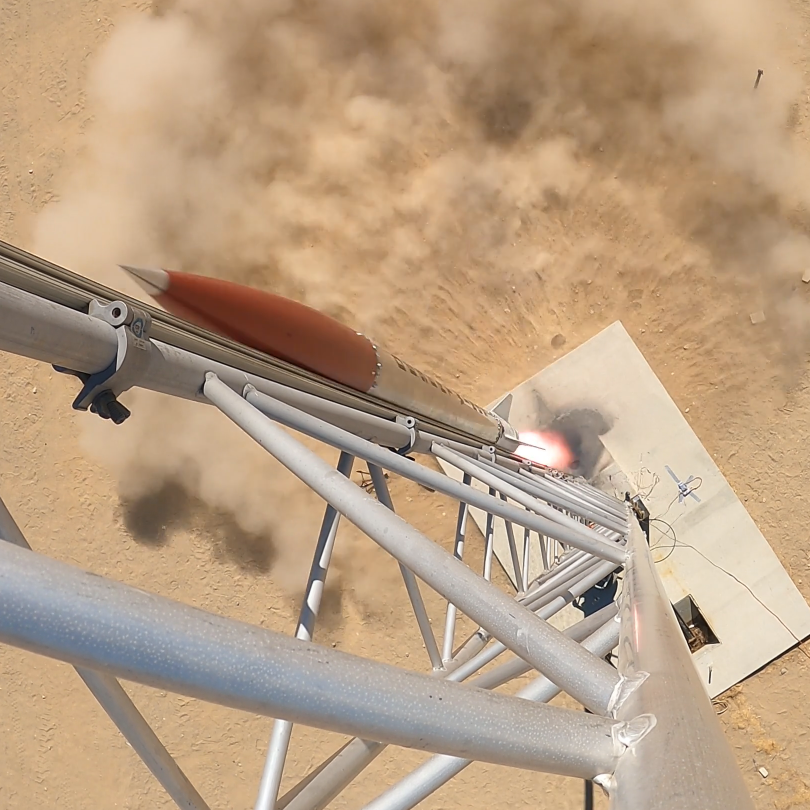
Desert Winds achieved an altitude of 26,879ft, breaking the current European altitude record for student liquid fuelled rockets
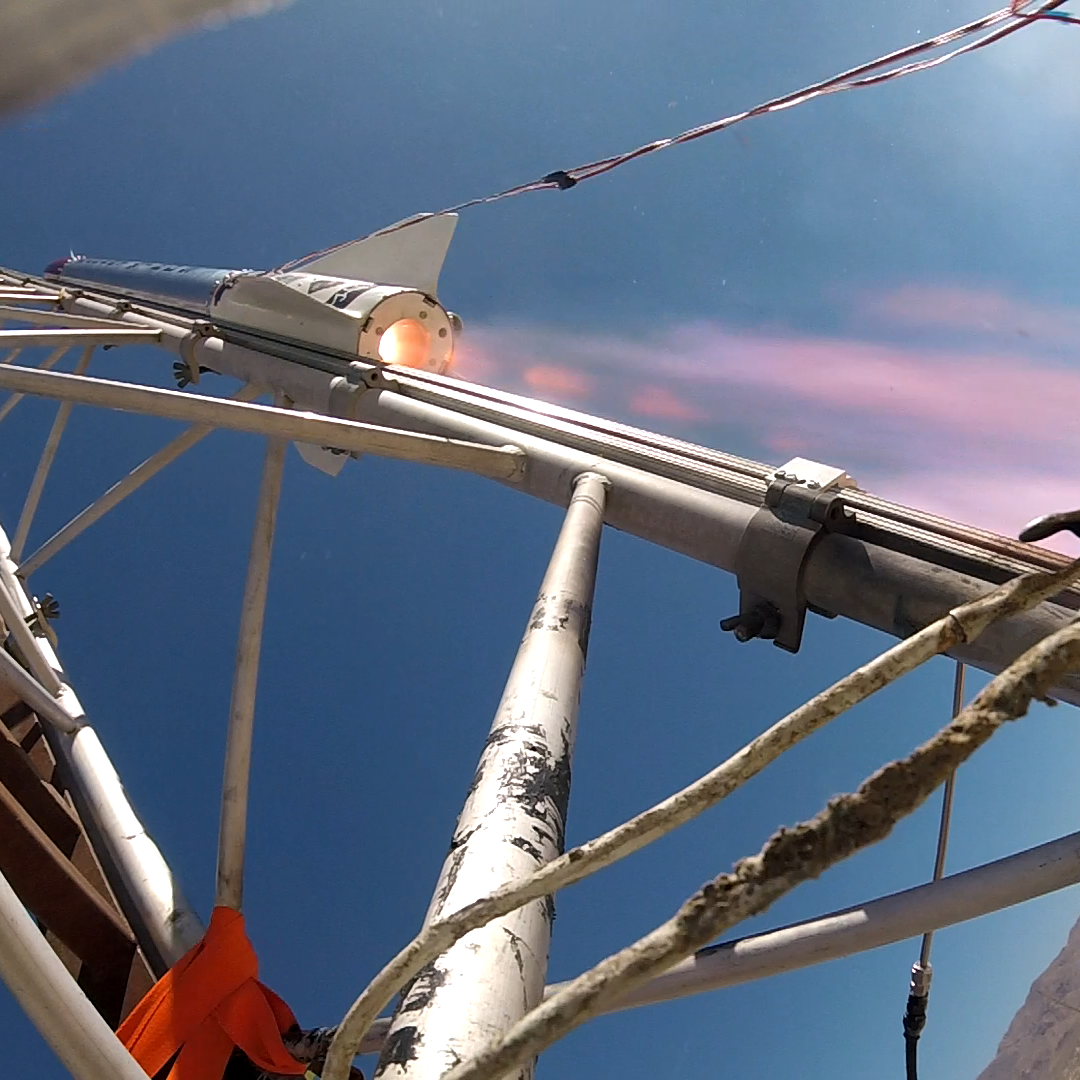
The team designed, built and launched the rocket in under 6 months, demonstrating an extremely rapid timeline.
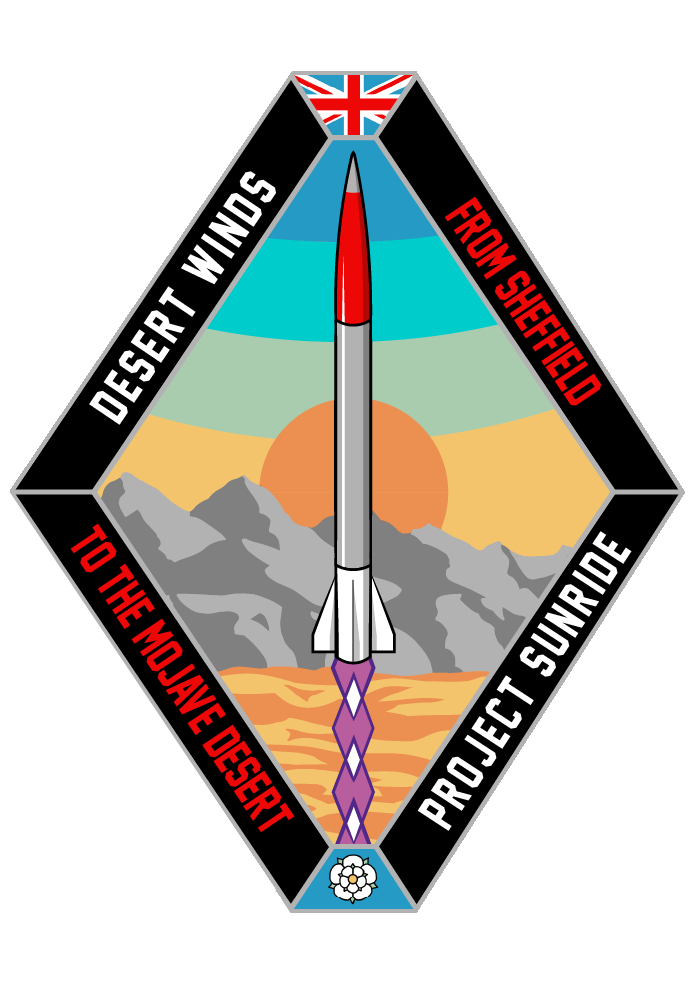
Mission Patch
About
Project Sunride have broken the European altitude record for liquid rockets. The launch signifies the first liquid rocket launched by students in the UK. The rocket went supersonic and reached an altitude of 26,879 ft.
The students designed and built their own rocket engine, Sunfire III. This engine was tested in March of this year, producing almost half a tonne of thrust. The engine was 3d printed with an aluminium alloy and is regeneratively cooled.
The rocket was launched from the Friends of Amateur Rocketry launch site in the Mojave Desert, California.
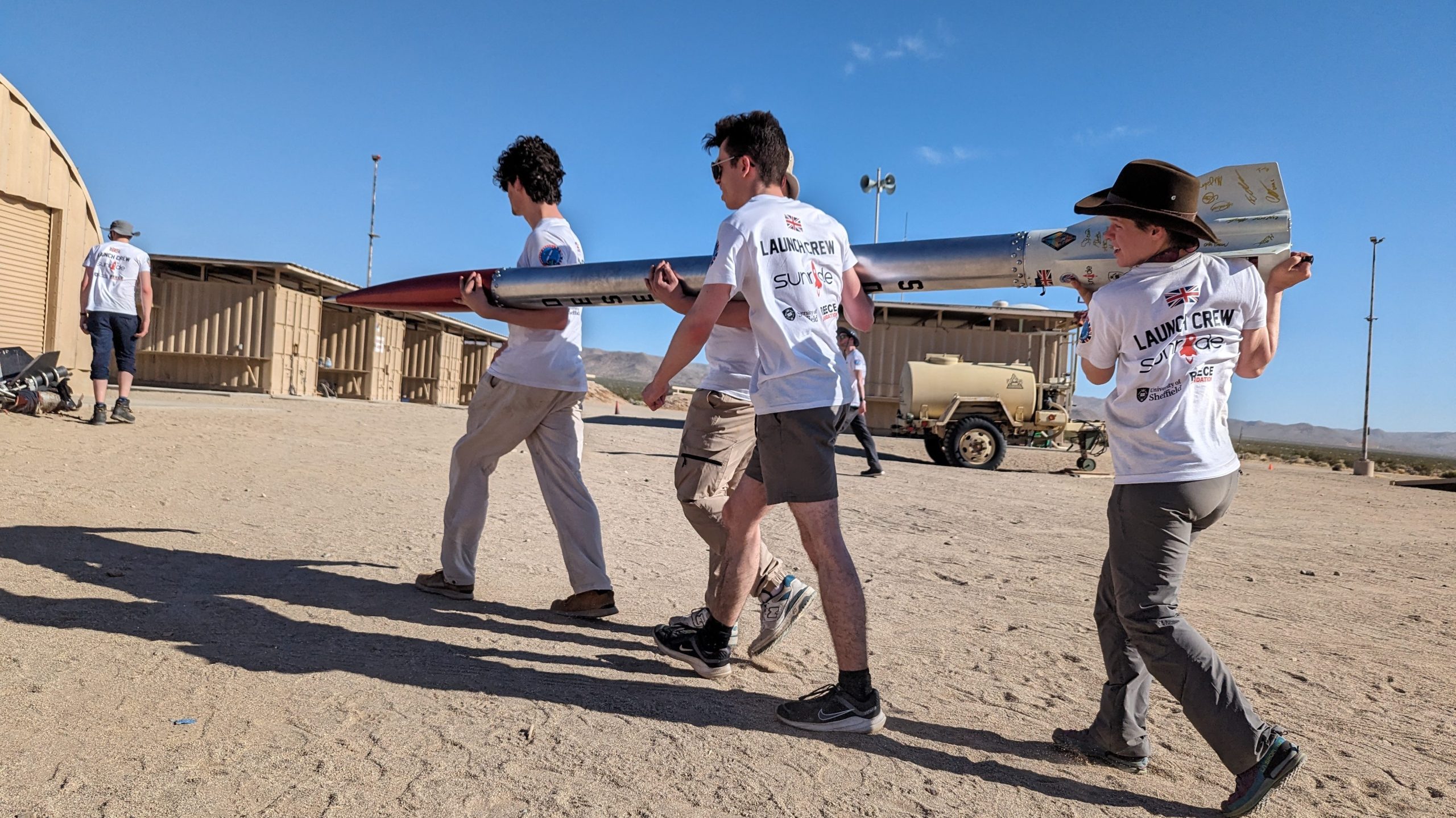
“I couldn’t be prouder of the Project Sunride team. In less than a year they have gone from hot firing their first engine to breaking UK and European records. When the team first asked me to support their dream, I had no idea how far they would come in such a short space of time. Everyone at Sheffield is incredibly proud of them”
Dr Alistair John
Programme Lead, Aerospace Engineering, University of Sheffield
Testing
Engine hot fire – 14th March 2024
The “Sunfire III” rocket engine, that powers Desert Winds, was hot fire tested on the 14th March 2024
The test was completed at Airborne Engineering Ltd in Westcott, UK.
- Test 1: 3.6kN burn for 2 seconds
- Test 2: 3.8kN burn for 5 seconds
- Test 3: 4.4kN burn for 3 seconds
Many thanks to Aconity3D GmbH for their support and printing the engine in their AlSi10Mg performance alloy!
First cold flow test – 24th April 2024
In April 2024, the first cold flow test was carried out at the University of Sheffield’s blast test site in Buxton, UK.
The goal of the test was to make sure the feed system performed as expected. The rocket used a concentric tank piston design for the feed system, where the fuel tank is located inside the oxygen tank.
This eliminated the need for a pressurant tank, simplifying the system. The vapour pressure of the nitrous oxide pushes on a piston, which in turn pressurises the fuel.
For this test, carbon dioxide and water were used as “analogue propellants”. This reduced the cost of the test and allowed the test to be completed safely.
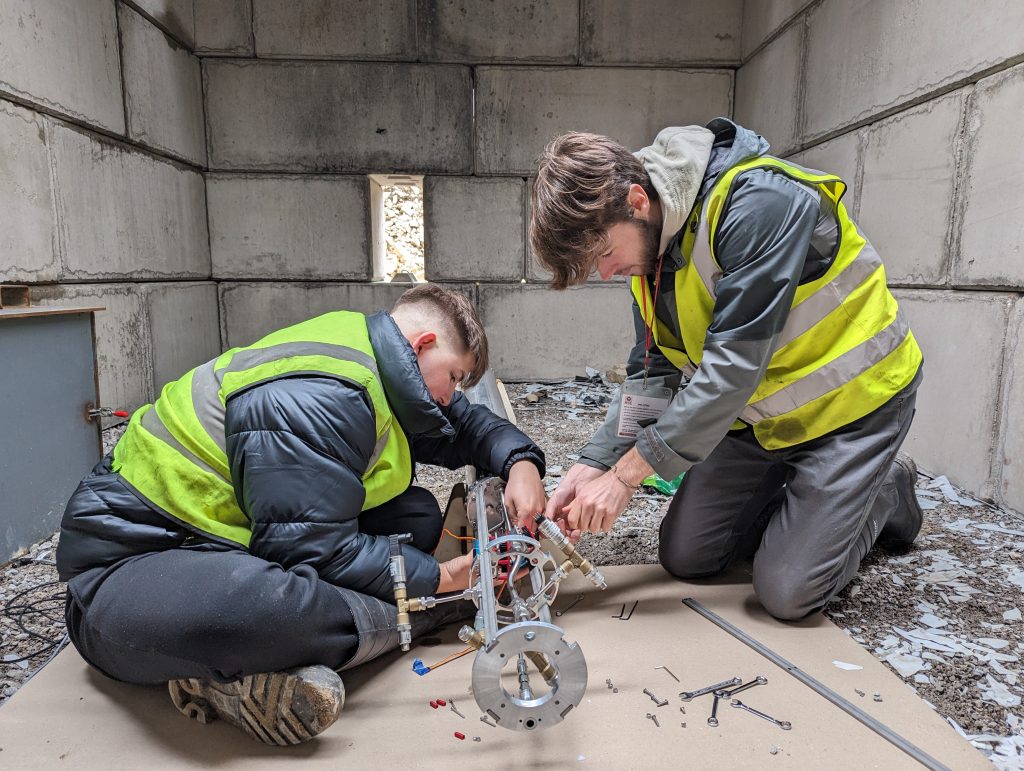
The team started the test day by performing a hydrostatic test of the system, proving that it could withstand pressures of above 70 bar for 30 minutes.
After that, the team performed the first cold flow test, shown in the video.
One of the valves was opened early in the test sequence and then during the test, the piston was jammed. This caused the fuel tank to compress, from the external pressure of the oxidiser.
The team learnt many lessons from this test, which were built upon in the next test.
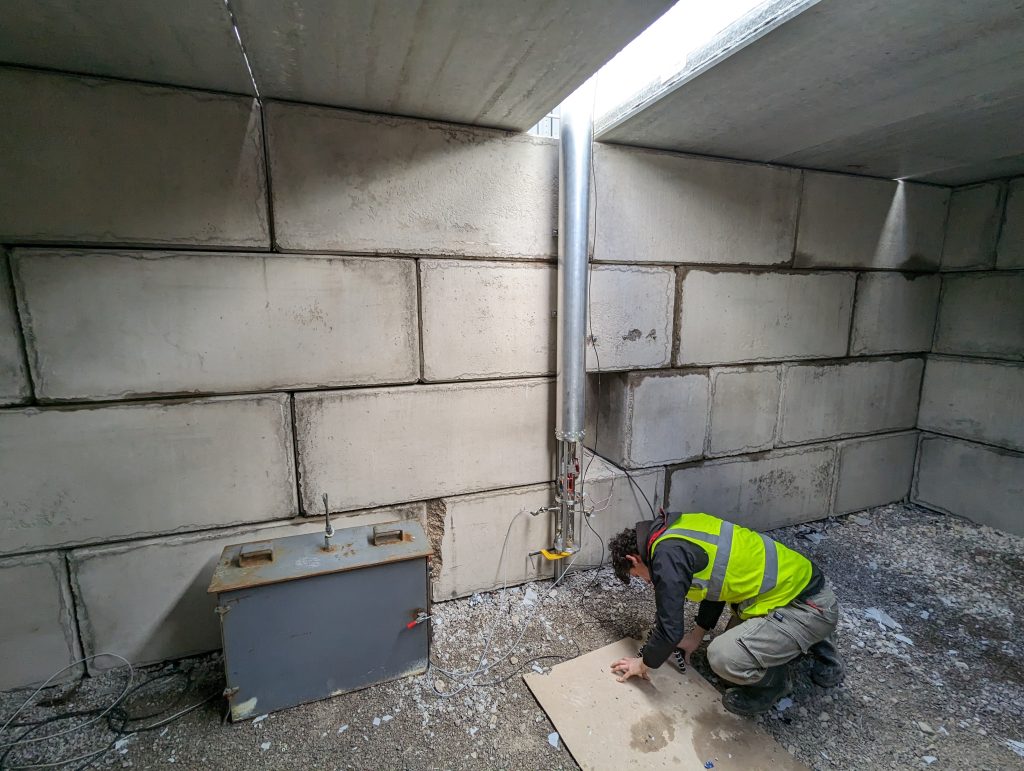
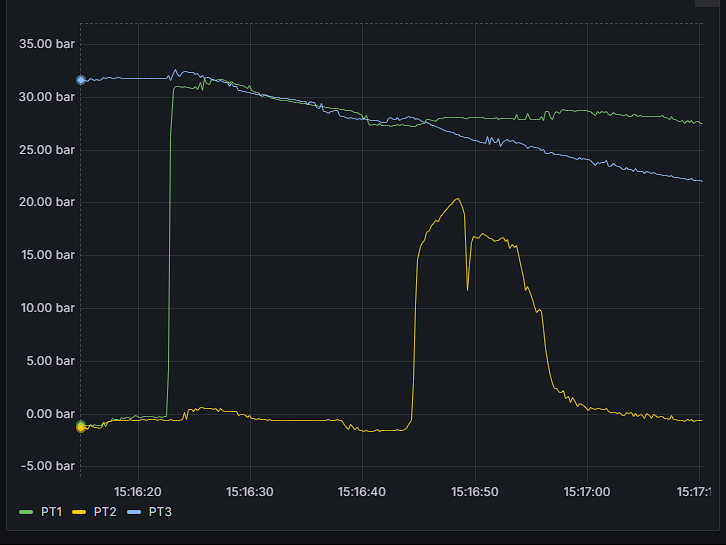
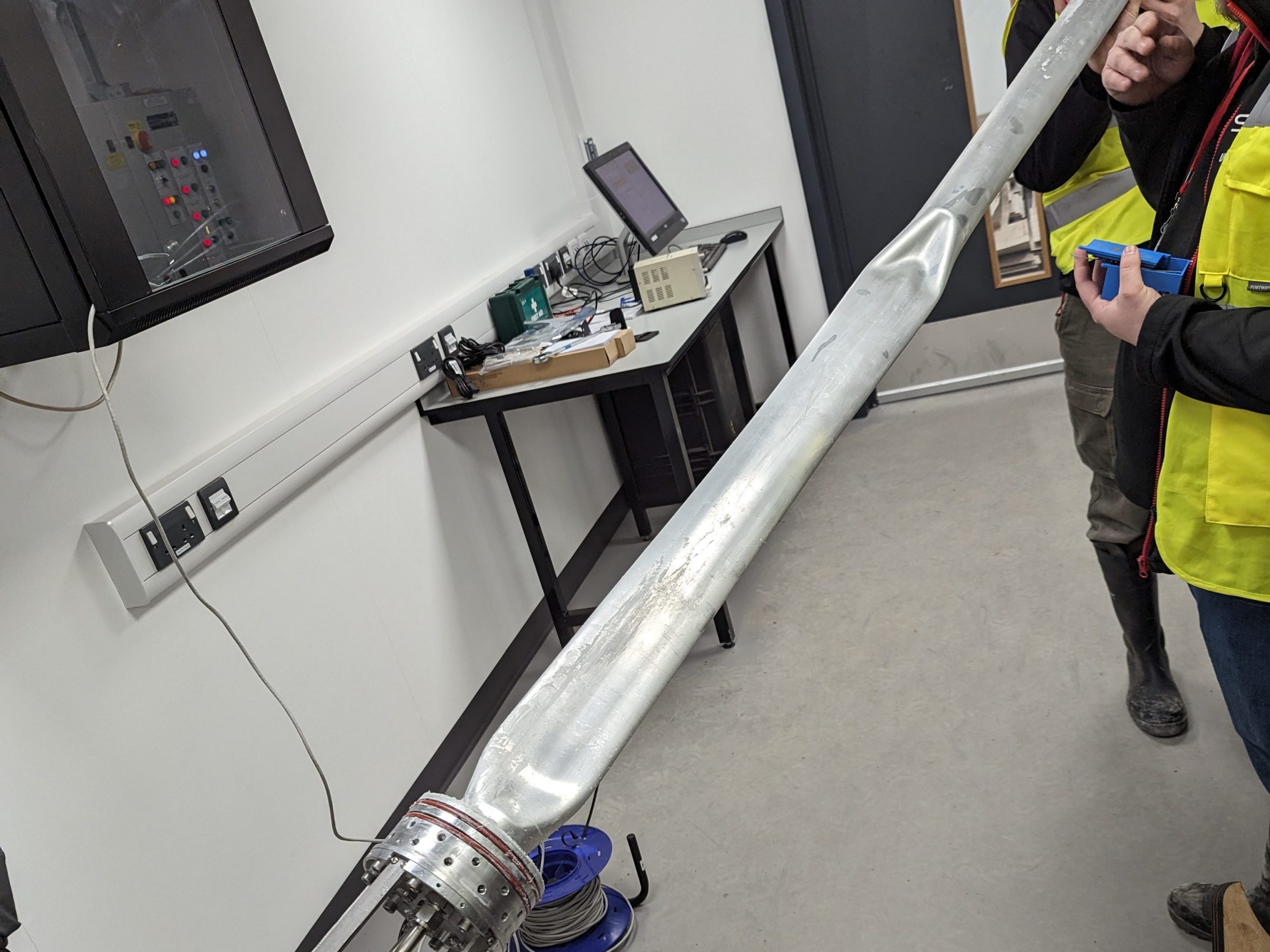
Second cold flow test – 16th May 2024
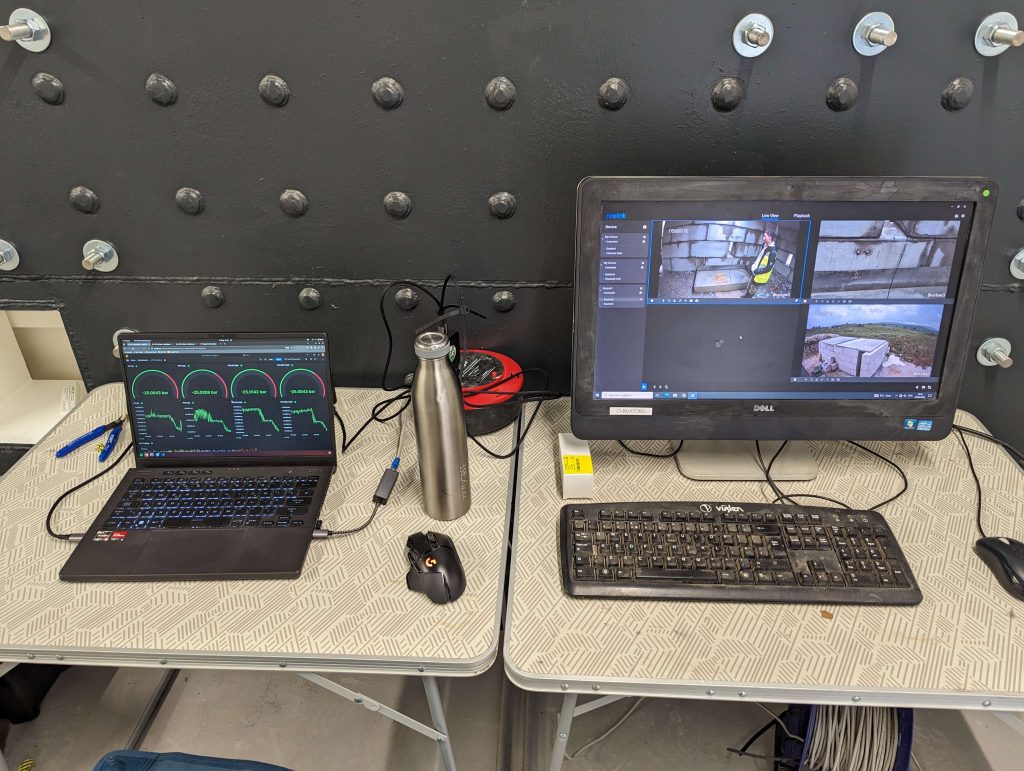
For the second test, a new, longer piston with added “wear rings” was made to reduce the chance of it jamming.
The control of the test was performed from one location to improve team communication, reducing the chance of an operator error
The test was a success, meaning the rocket was ready for launch
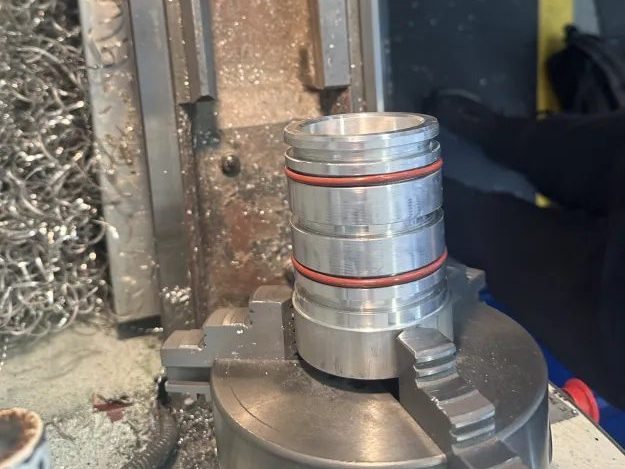
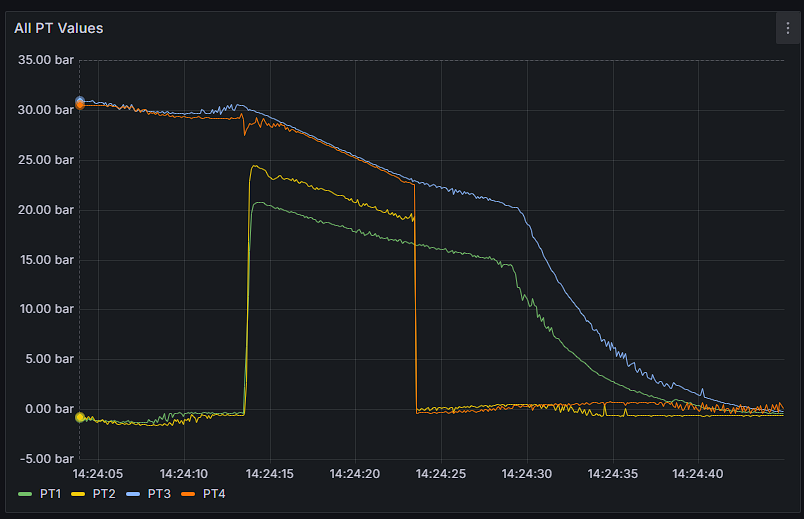
PT1 = Ox, PT2 = Fuel, PT3 = Ox Tank, PT4 = Fuel Tank
Launch
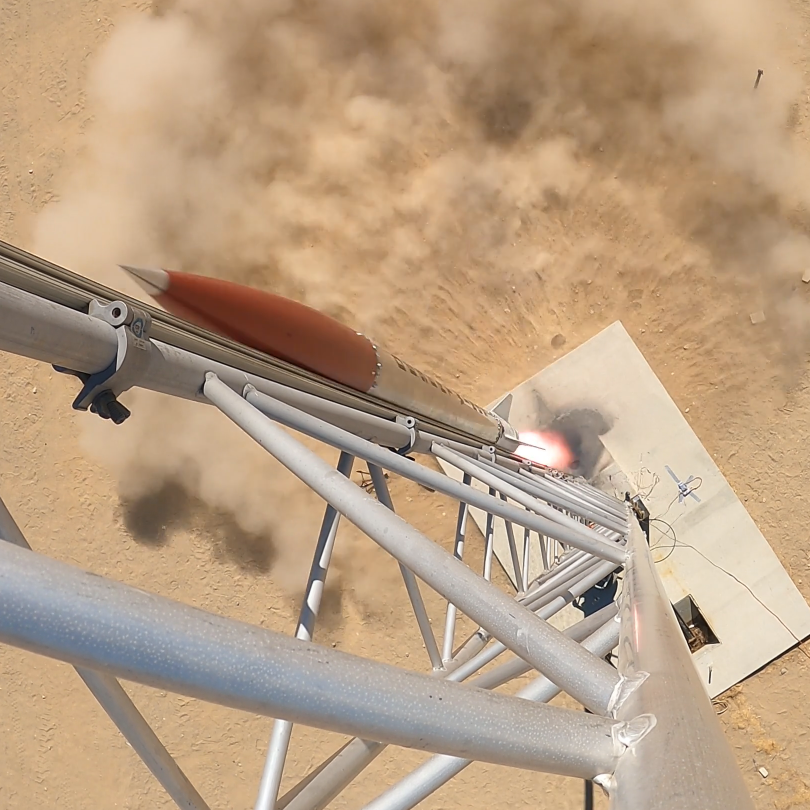
DOCUMENTARY COMING SOON